Introduction of Concrete
Concrete is a long-lasting construction material made of Portland cement, aggregates (such as sand or gravel), and water. Concrete is prepared by mixing together these materials to form a slurry that hardens over time to create a solid mass that is capable of withstanding massive amounts of load and environmental conditions. It is the most widely used construction material worldwide. It provides strength, versatility, and durability, making it a key component in building foundations, pavements, structural elements, decorative finishes, components, and others.
Admixtures are also added during the mixing of the concrete to improve special properties of concrete and meet special requirements. They can alter the setting, hardening, strength, and durability of the concrete.
Curing of concrete
Curing freshly laid concrete is critical to its strength and endurance. The sequence of setting, hydration, and crystal formation should not be disrupted, especially within the first 48 hours for type III early-setting Portland cement. This is twice as lengthy as the general-purpose type I requirement. The cement surface should never be allowed to dry, as this implies a lack of water for the hydration process. If the surface gets dry, there will be inadequate water for the hydration process, resulting in a significant drop in the quality of the concrete. It is possible that frequent sprinkling is required. In hot, dry weather, the forms may need to be left in place and the exposed surfaces covered with a sheet of polyethylene or another appropriate material.
Composition of Concrete
Water & Cement
The compressive strength of the concrete entirely depends upon the smaller ratio of water to cement. If the water contains impurities and it is not fit for construction use, then it can destroy the concrete and affect its strength and its setting time. It also leads to corrosion of the reinforcing steel, which is present in the concrete. Drinkable water is available for the concrete.
Concrete in construction porosity causes both physical and chemical degradation. Some porosity is to be expected. Aggregates can be a significant cause of porosity if their size distribution is not consistent. If the aggregates are not dispersed consistently in size, the gaps between them will fill with water and air. Excess cement paste will be required to fill the spaces between the particles, cementing them together and maintaining the strength of the concrete. The optimal aggregate form for a better fit and optimum concrete strength is cubical, flat, or elongated with a rough surface for improved adherence. They should not be rounded or smooth.
Aggregates
Aggregates account for approximately 75% of the total weight of concrete. Although considered a low-cost filler, aggregates add strength to concrete because they are often stronger than the cement that holds it together. Particles should be graded in size for the optimum outcomes so that the aggregates can fit snugly together to produce a robust, densely packed structure.
Admixtures
Admixtures are chemicals added to concrete to modify its physical properties. An admixture often affects more than one property, so side effects must be considered if they are used. For example, water-reducing agents increase workability and can act as set retarders. Water reducers can also increase the early strength of concrete.
The common type of admixtures are:-
High-range superplasticizer water reducers
Admixtures containing superplasticizers are also known as super fluidizers, super water reducers, and high-range water reducers. Their action is similar to that of a surface-tension reduction agent (surfactant), in that it breaks apart cement aggregates into smaller groups of suspended cement particles, causing the cement mixture to become more fluid. Because they improve the flexibility and workability of concrete mixes, this family of admixtures has been dubbed “superplasticizers.”
Accelerators
Accelerating admixtures assist to restore more typical settings and early strength times in cold conditions. Accelerators compensate for the lower ambient temperature and therefore slower pace of reaction. Early strength and set development do not guarantee later strength. Other desirable features may also be diminished.
Retarder
A set retarder is a chemical additive that increases the workability and setting time of concrete. Set retarders can compensate for the quick setting caused by the increase in temperature when operating in hot areas, but they are only useful during the first week of setting. Concrete accelerator’s give early strength. Water reducers and retarders use similar substances and achieve comparable outcomes.
Air-entrainment agents
Entrainment agents, such as surfactants, act as emulsifiers and foaming agents to improve the plasticity and workability of the water paste. They also reduce bleeding by stabilizing the gelatinous mixture (Source: Time-Saver Page no. 127-128)
Construction with concrete
Reinforced concrete
Steel bars (re-bars) and steel cables can be used to reinforce concrete in prestressed concrete. To promote mechanical adhesion, re-bars have lugs (deformations) at regular intervals. Concrete was originally thought to shield steel from corrosion by keeping moisture and oxygen out. Instead, corrosion is slowed by the steel’s passivity as a result of the alkalinity of the concrete.
Prestressed Structure
Pre-stressing concrete is a method of compensating for the low tensile strength of concrete. A prestressed beam is created by extending a high-tensile wire along the length of a concrete form. The cable is then tensioned and stretched using jacks at either end. High-strength concrete is poured into the shape around the cable. As the concrete hardens, it forms a connection with the cable. When the jacks are removed, both the cable and the concrete beam retain the proper tension.
Method of forming prestressed concrete
Post-tensioning the cable is another way of creating prestressed concrete. Before the concrete fills the form, the cable must be wrapped in a thin steel or paper tube (inside the form) and fastened at the ends. After the concrete has cured, jacks at the ends of the beam or structure may be used to tighten the cable. This can be done after the beam has been installed on the job site. Finally, the prestressed concrete beam is completed by filling the tube with grout.
Polymer concrete
Polymer concrete (Portland cement replaced by a polymer) has a lower rate of water absorption, higher resistance to cycles of freezing and thawing, better resistance to chemicals, greater strength, and excellent adhesion qualities compared to most other buildings materials. The most commonly used resins (polyesters and acrylics) are mixed with the aggregate as a monomer with a cross-linking agent (a hardener) and a catalyst to achieve full polymerization. Polymer concrete in construction is usually reinforced with metal fibers, glass fibers, or mats of glass fiber. The use of polymer fibers (such as polypropylene) as a replacement for asbestos in cement has received much attention. (Source: Time-Saver Page no. 129)
Properties of Concrete
- Energy efficiency
- Fire resistance
- Earthquake safety
- Durability
- Porosity and density
- Thermal and acoustic insulation
- Impact resistance
- Elasticity
- Segregation
- Bleeding
- Fatigue
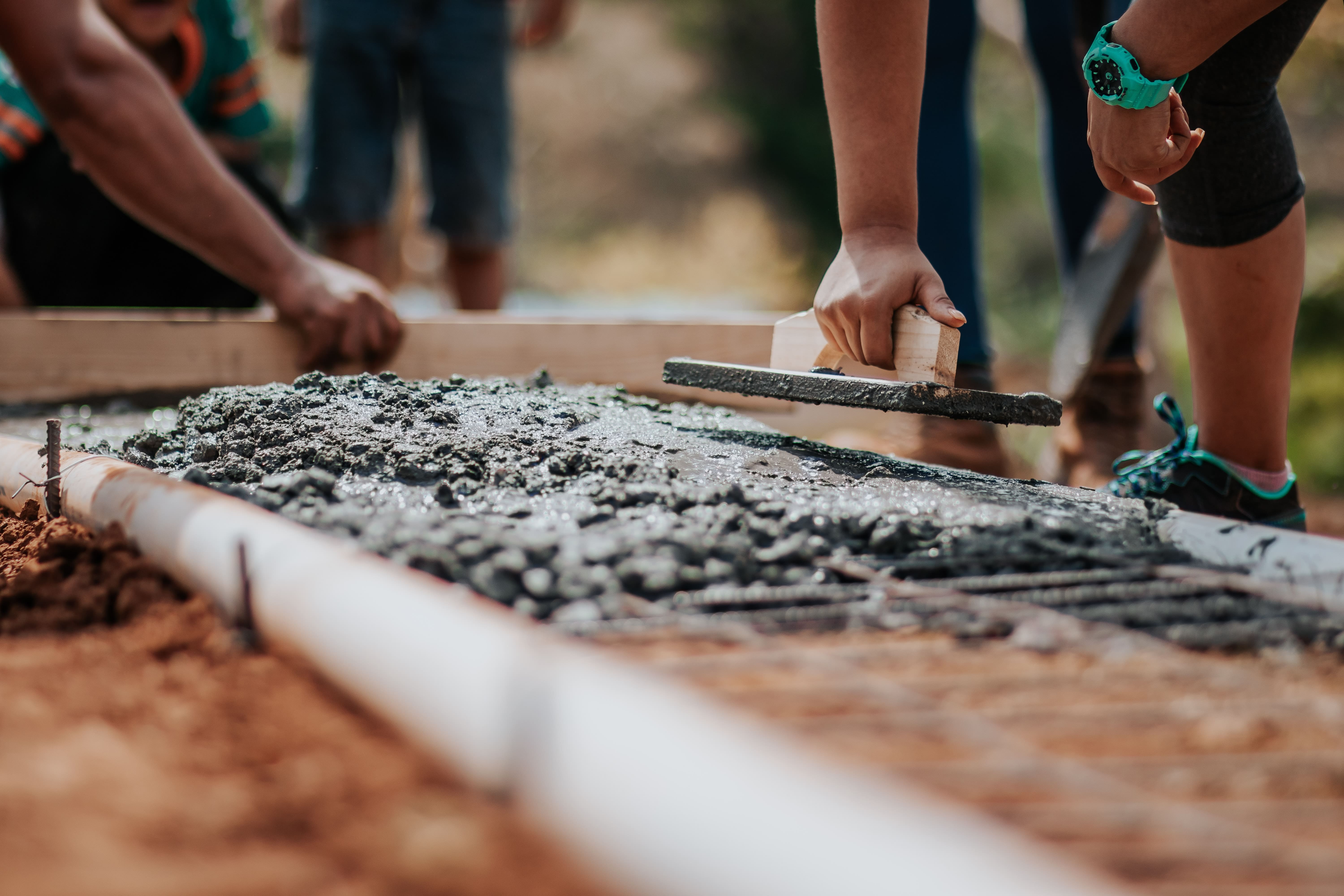
Concrete: common problems and corrections
Some of the common building problems related to concrete as listed here with their causes and suggestions for correction.
- (Problem) Sulfate deterioration of concrete is caused by moisture and sulfate salts in the soil that is in contact with concrete foundations, floor slabs, and walls.
- (Correction) Type V sulfate-resisting cement is made for this purpose. To correct the problem (if the soil cannot be kept away from the concrete in construction), better drainage might keep the soil dry and the salts in solid, not solution, form.
- (Problem) Efflorescence is the appearance of an unsightly fluffy white crust on the surface of walls. It is caused by salts in solution (in the concrete, the stone, or the bricks) moving to the surface of an interior or exterior wall. As the water evaporates from the salt solution in dry weather, a loose mass of white, powdery salts remains.
- (Correction) Some relief from efflorescence can be gained by treating the surface of the wall with a water repellent and sealing all cracks and joints to keep out the rain.
- (Problem) Freeze-thaw cracks (forming in concrete in subfreezing weather) can be caused by concrete with a water/cement ratio that is too large. This can produce tiny crevices and voids around the aggregates, allowing penetration of water into the concrete by wind-driven rain. Tremendous forces, produced by the expansion of water as it freezes to form ice, cause spalls (flakes or chips) and cracks in the concrete in construction.
- (Correction) It requires waterproofing the surface of the concrete with a polymer-modified cement-based surface coating. Further protection could be gained by applying a protective coat of paint
- (Problem) Leaks in concrete roofs or parking decks are due to water penetrating the surface. A waterproof coating alone rarely works because the cracks continue to grow.
- (Correction) A solution is to use epoxy in the clean cracks and fill them with a flexible sealant material.
- Corrosion of steel re-bars can cause cracks and rust stains to appear in the concrete. (Source: Time-Saver Page no. 129-130)